Maroso autoclaves are pressure chambers specifically built to guarantee the optimisation of the different processes carried out through the constant control of the temperature, pressure and vacuum parameters during the whole cure cycle, in absolute safety and respect of the operating conditions.
Our autoclaves guarantee the cure cycle repeatability and machine reliability through time, thanks to the use of quality components both in the mechanical and electronics part, avoiding the machine downtime. Maroso autoclaves are built with certified materials and in accordance with the most advanced technologies, which guarantee maximum operating safety, energy saving, long duration and ease of use. Furthermore, an alert appears on the machinery graphic interface to signal the maintenance need, after n cycles or a certain amount of working hours.
The company organizational structure allows to provide a full activities package: the autoclave position is studied together with our technical staff according to the factory layout and factory systems, providing a turn-key service. Moreover, Maroso offers a remote technical assistance without many long waits.
Tailor-made machineries
All Maroso autoclaves are designed and built in accordance to the customer’s specific requirements. The aim is to provide a machinery able to meet any customer’s need, since the smaller details. We follow the customer throughout the whole process thanks to the constant direct contact with the technical staff. Maroso is able to manufacture autoclaves of different sizes; especially, our productive range includes the production of autoclaves with useful diameter from 1m to 4,2m and beyond; the length instead can exceed 15m.
In addition our autoclaves, thanks to the possibility of interconnection in the Industry 4.0, allow to create ad advanced factory that goes beyond the normal factory limits.
Autoclaves for composites
Autoclaves for composites, allow the lamination of different materials to obtain an heterogeneous combination with various advantages and dissimilar physical properties compared to the initials, improving the original limits. Composites have many advantages: corrosion, wear and impact resistance, duration to the fatigue, lightness and the electrical insulation improvement. Their use lead to a significant technological progress in many sectors as the aerospace, automotive, rail, naval, construction, wind and sport and leisure. The transformation of these materials is carried out in Maroso autoclaves, which are pressure tanks, that designed in accordance to the customers’ requirements allow to obtain an high-performance product through the modification of the environmental physical properties as pressure, temperature and vacuum inside the autoclave.
Maroso, by the use of process controllers and high-tech equipment, guarantees attention in the cure process, quality and long term repeatability.
The process data management is a system that allows the customer to have a synthetic and graphic management and vision of the machine cycle data, in order to have a correct process monitoring. Through a custom designed package is possible to obtain both the product and batch traceability, connecting the machine to the customer IT infrastructure for the data download in the server.
Controlled management of unexpected situations
During the normal productive process, unexpected situations as blackout or network instability could occur, due to external factors or temporary electrical overloads, causing negative consequences from the productive and the machine equipment point of view.
Over the years, Maroso developed technical solutions aimed to reduce to the minimum this events, for example by keeping a stable power voltage supply, properly tuned and filtered through UPS (uninterruptible power source) to preserve and extend the electronic devices life.
Allowing an uninterrupted cure cycle management even in case of temporary electricity lack, the process “freeze”, restoring at the electricity supply. The “freeze” phase allows the customer to preserve the treated material and to conclude its cure completely.
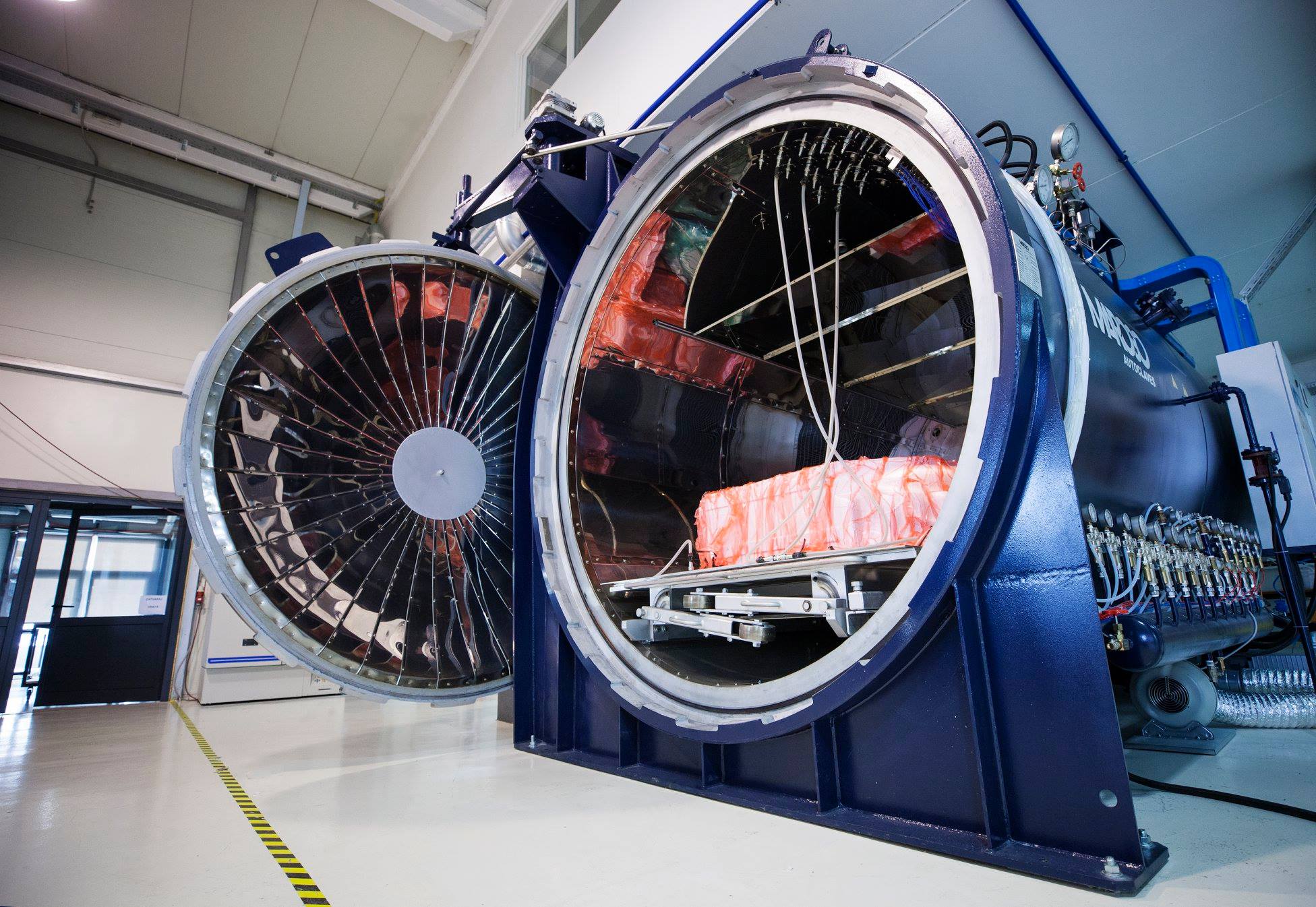
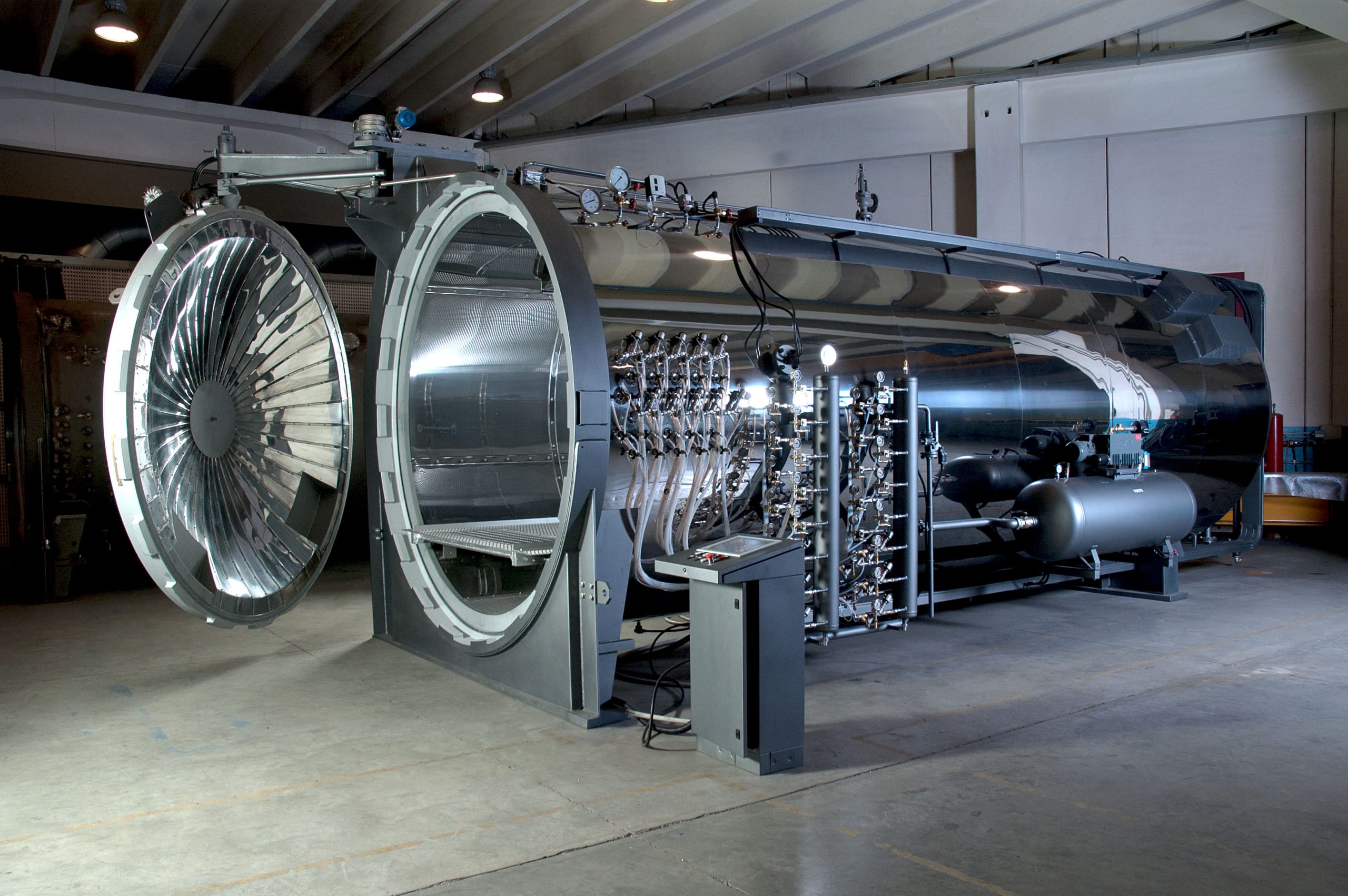
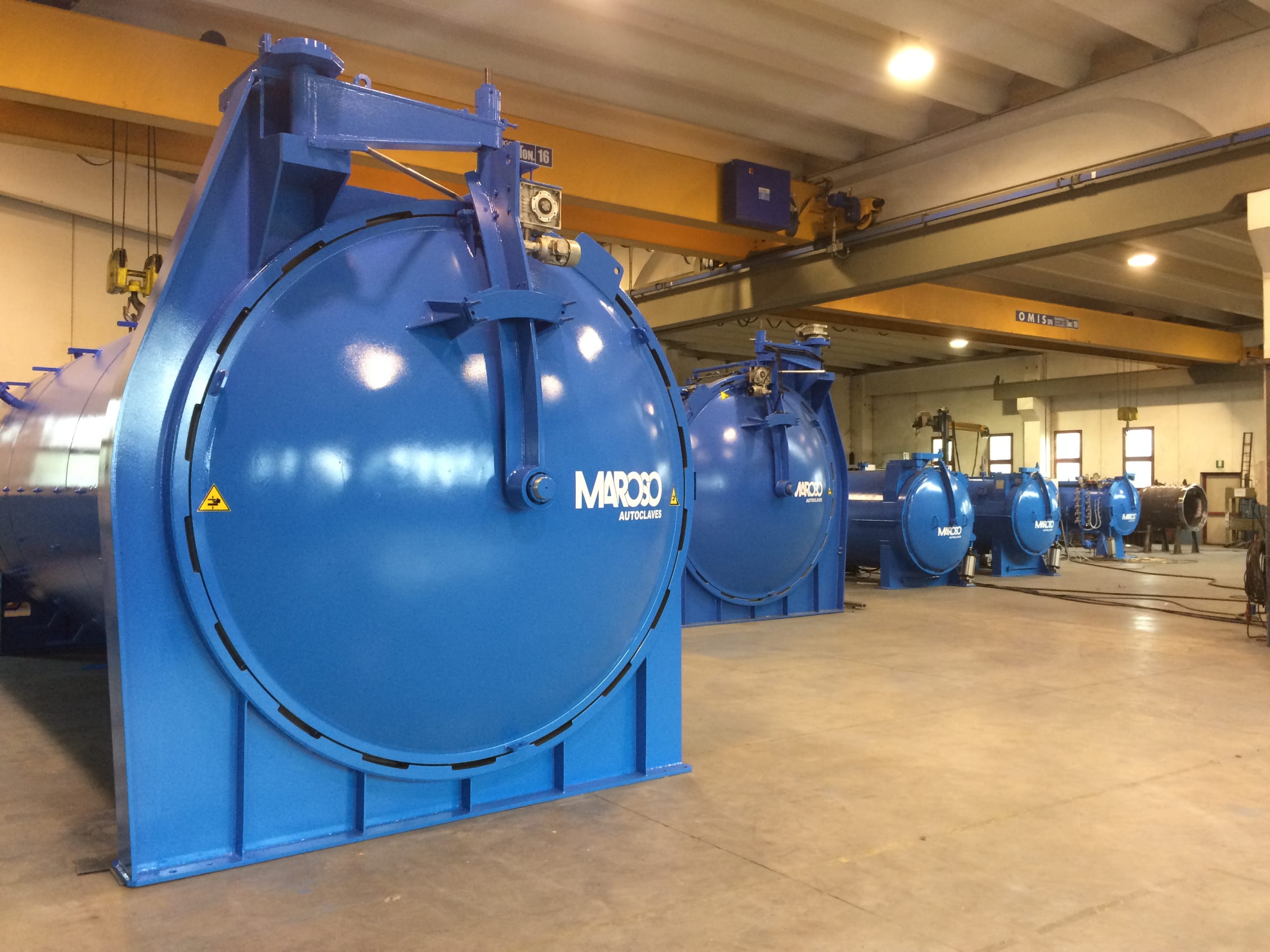
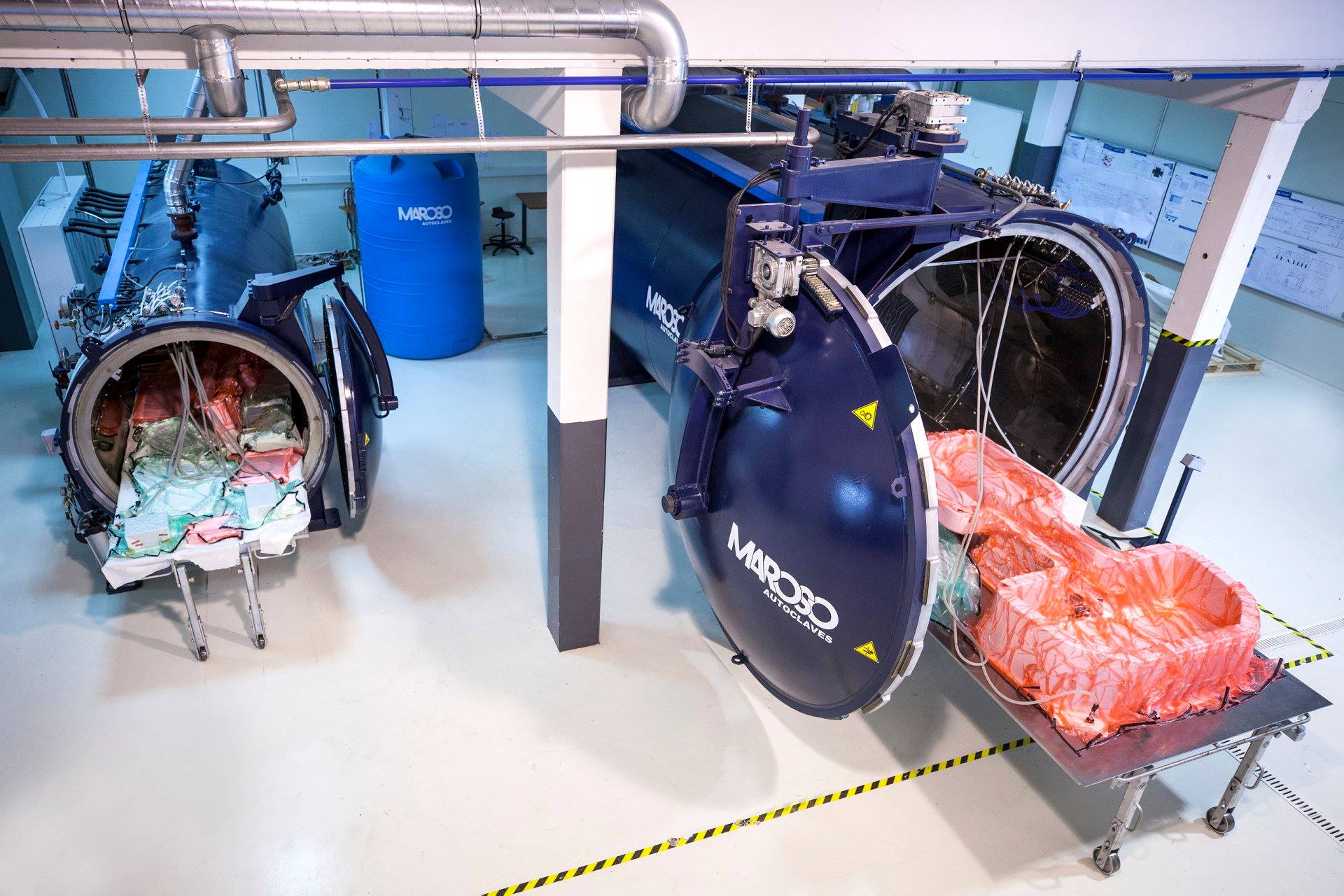
Autoclaves for Laminating Glass
Glass sector uses autoclaves for the laminating production of flat, curved and special glasses, both tempered and hardened.
The laminating process allows obtaining a composite glass, composed by 2 or more sheets of glass, by inserting a plastic or ionoplast interlayed material. Thanks to the control of the pressurization, heating and depressurization phases we are able to obtain a good quality laminating process. In case of blackout, the machine adopts technical solutions authorizing the cycle interruption and its later restoration, keeping the pressure and preserving the part integrity which is inside the autoclave.
Autoclave perfectly designed and integrated in the productive process.
Autoclave is designed in accordance to the customer’s requirements and is perfectly integrated in the laminating glass productive process.
- the machine positioning is optimised according to the factory spaces, the laminating lines and services;
- optimization of the machine thermodynamics design and the thermal exchange with the processed parts, in order to obtain the maximum performance with a low energy waste and a consequent consumptions reduction;
- correct vessel design based on the payload;
- <span”>design, supply and installation of the necessary services for the autoclave running (cooling system and pressurisation group, trolleys handling system, vacuum group, etc.);
- specific structural design according to the loading capacity: trolleys can be customized in shape, size or constructed with different loading solutions in order to take advantage of the autoclave internal spaces;
- Maroso autoclaves door opening system allows to reduce the space opening;
- machine connection to the customer’s IT infrastructure for the data download in the server.
Laminated glass produced with Maroso autoclaves is used in different fields, as: building, interior architecture, security glass ( as shatter-proof/burglary-proof, safety glass, bullet-proof, explosion-proof, fire-proof, hurricane-proof) and for the trucks and cars windscreen.
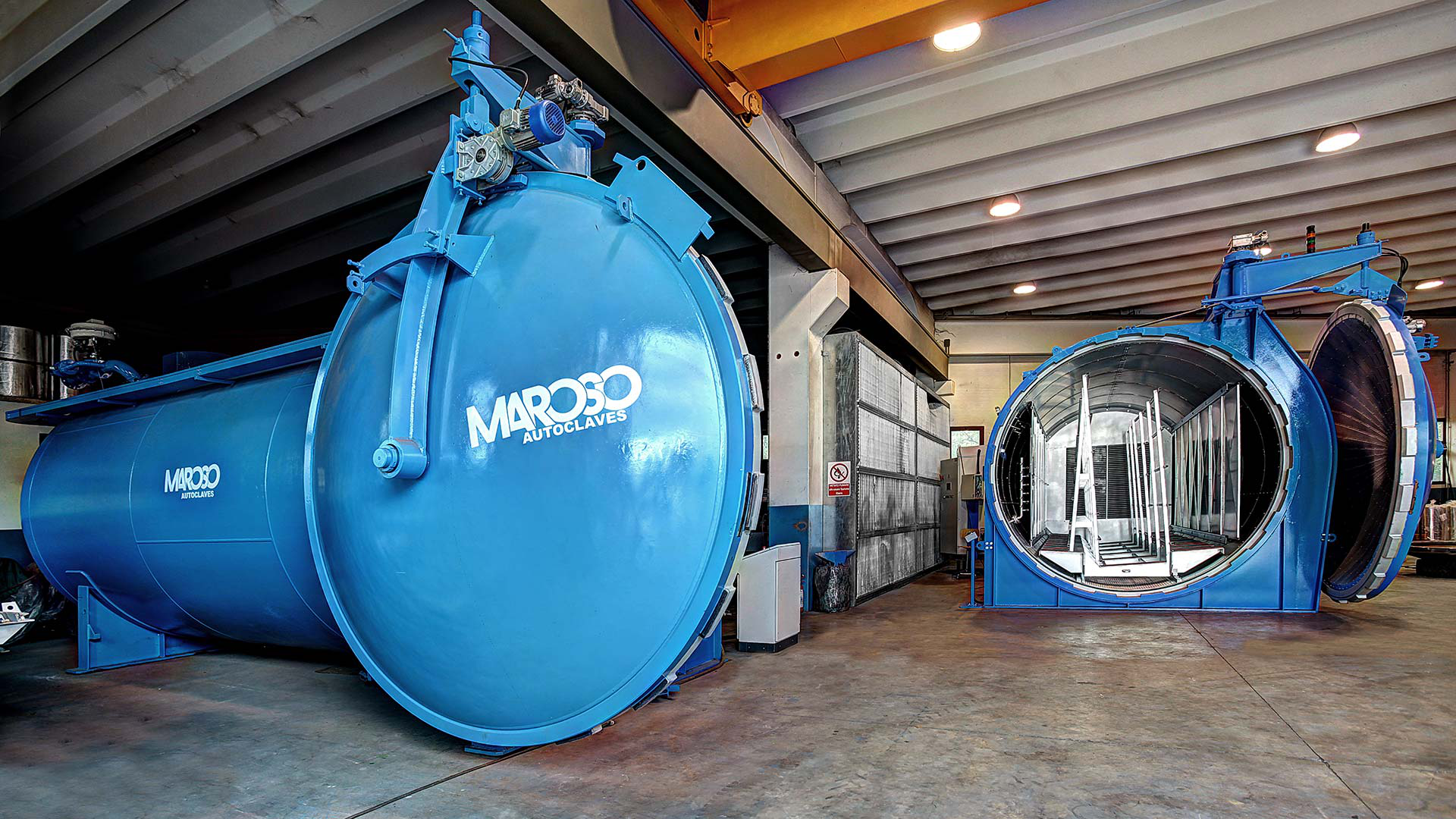
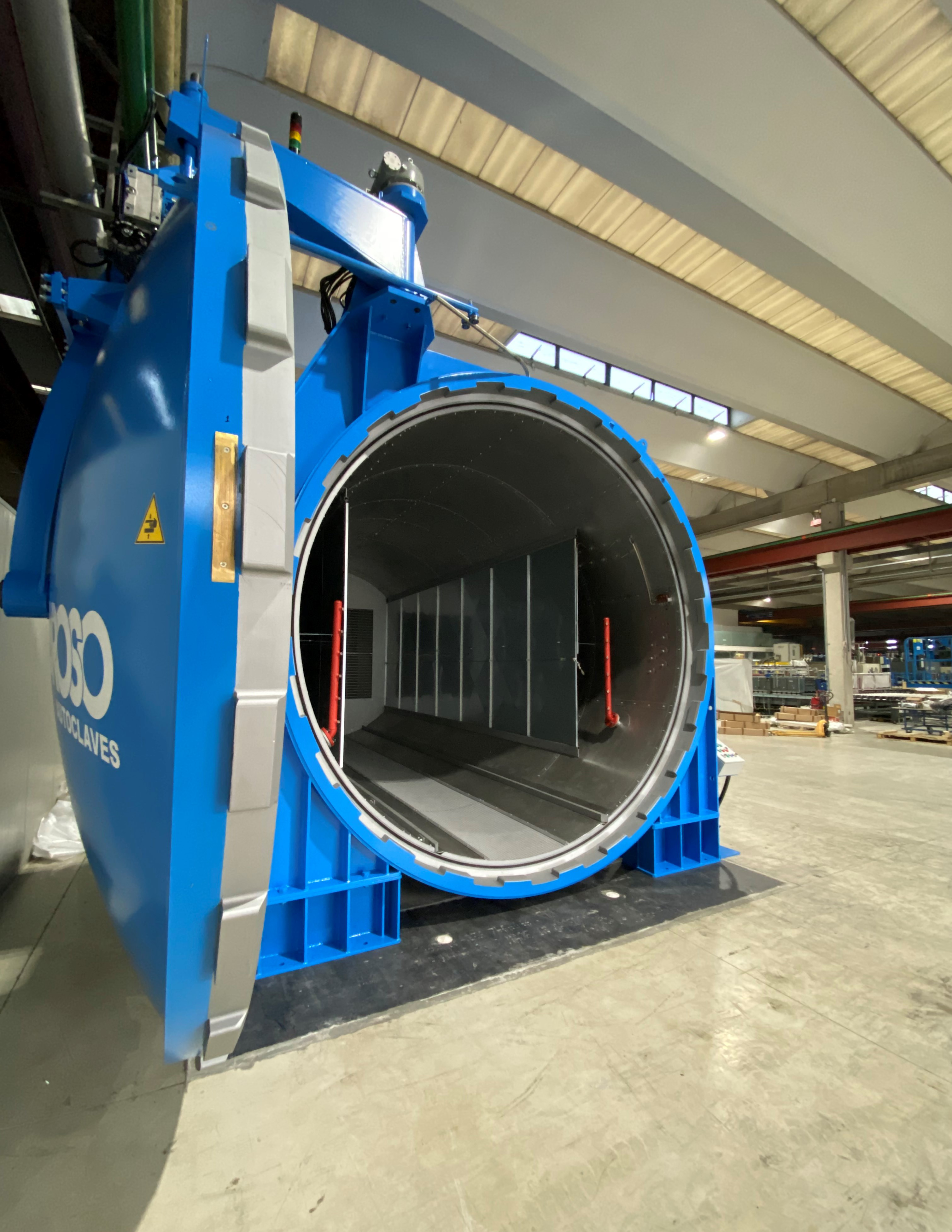
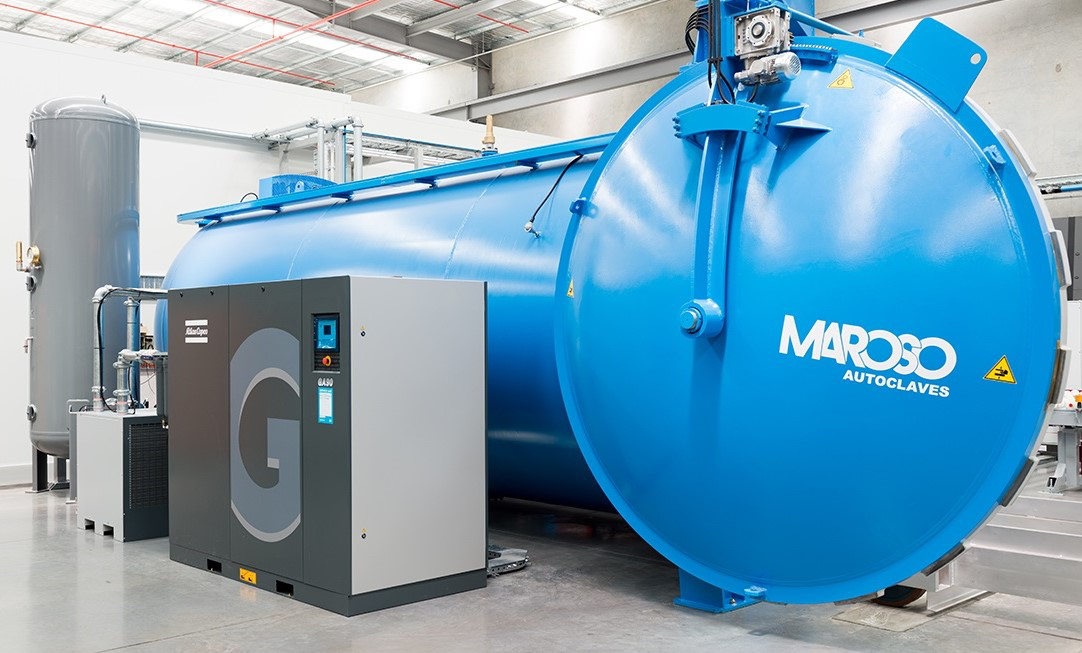
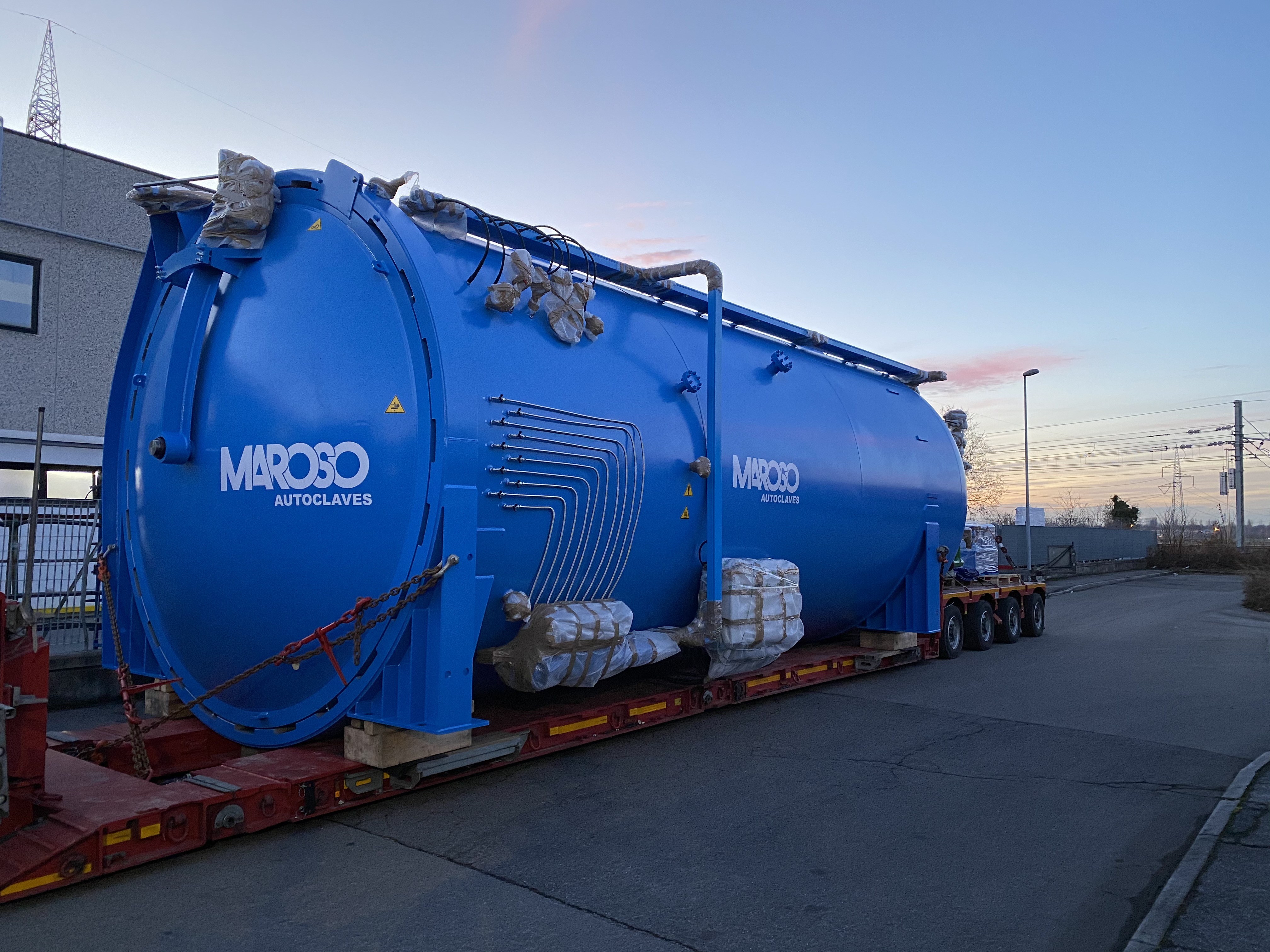
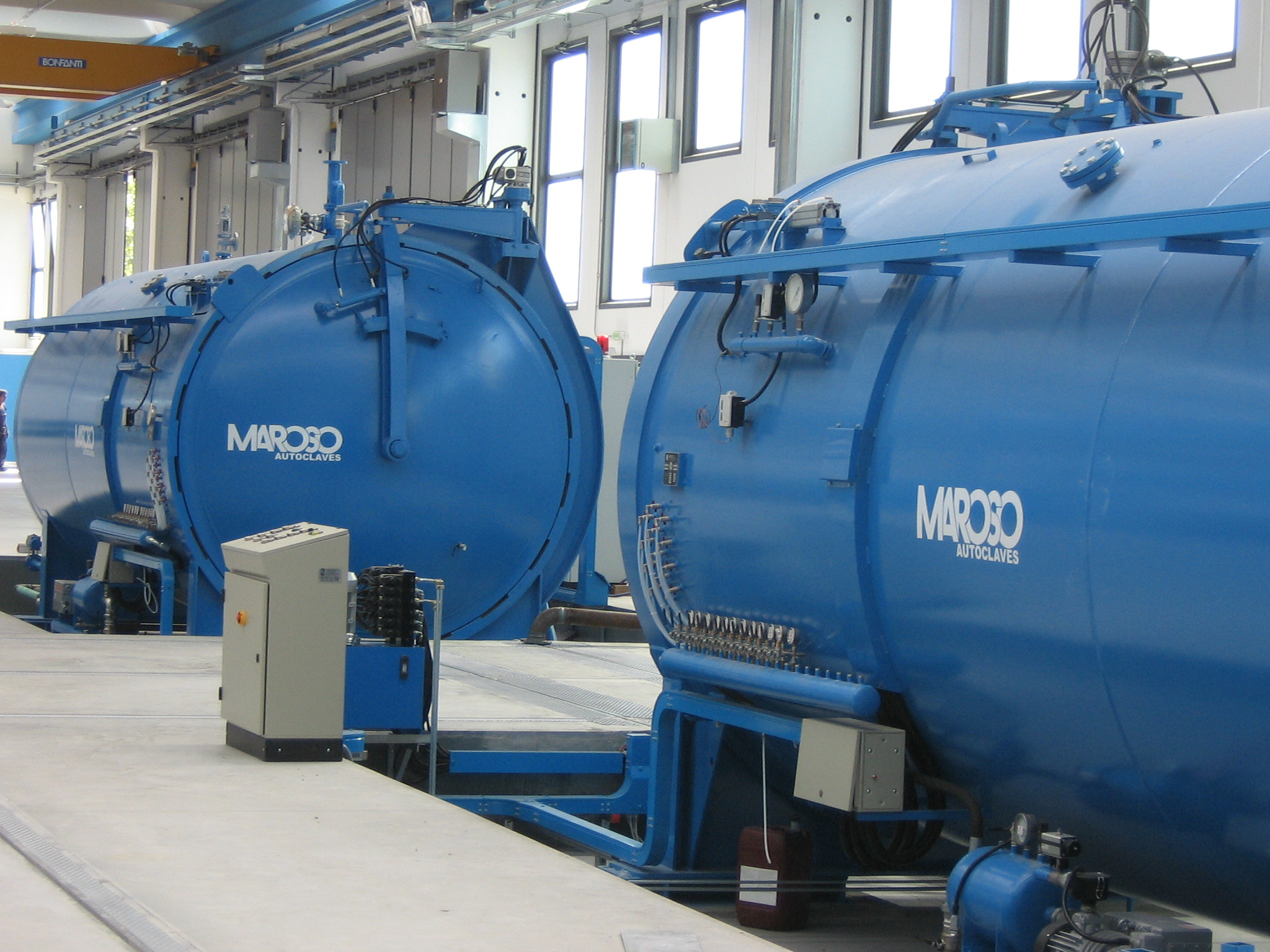
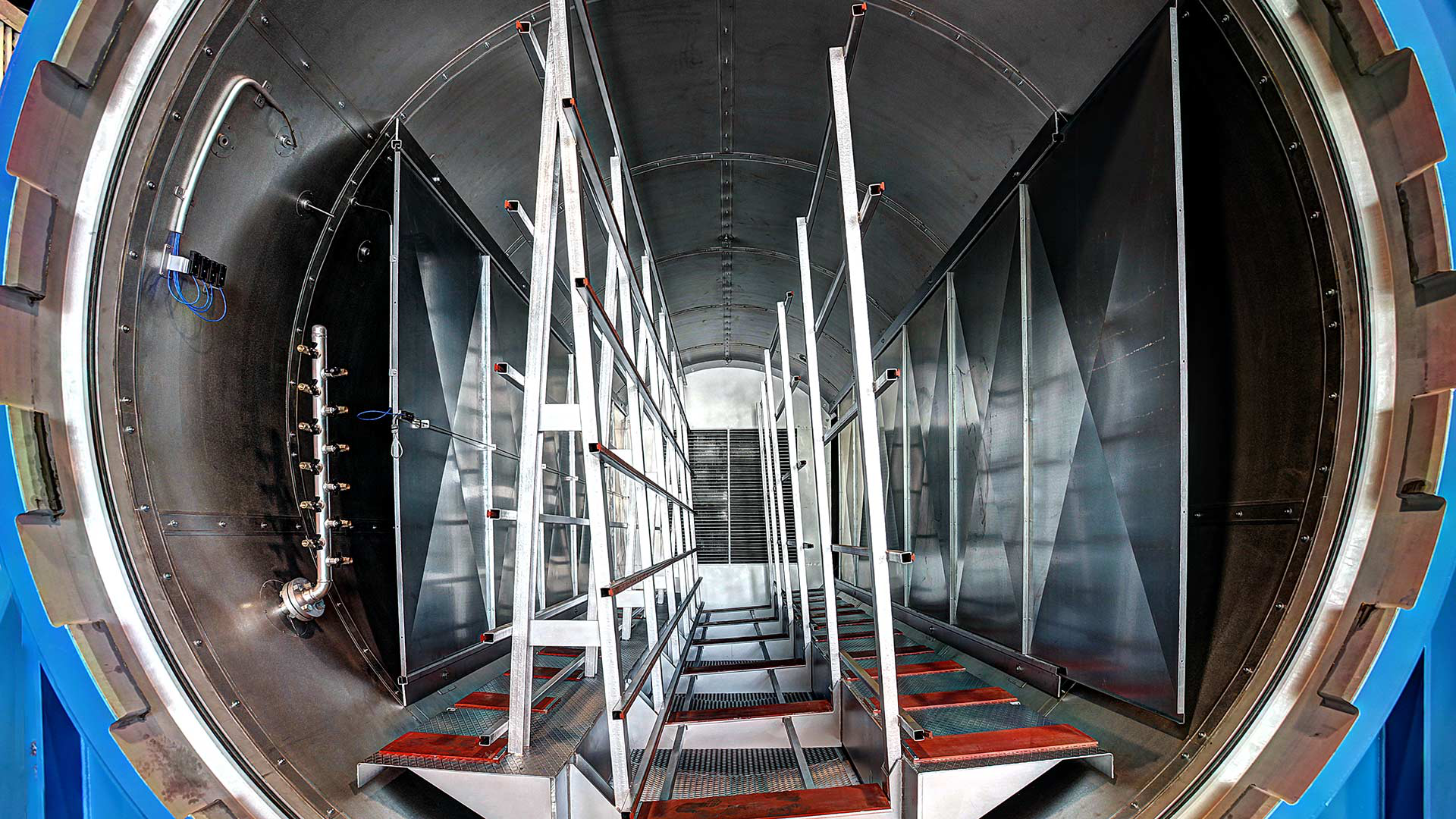
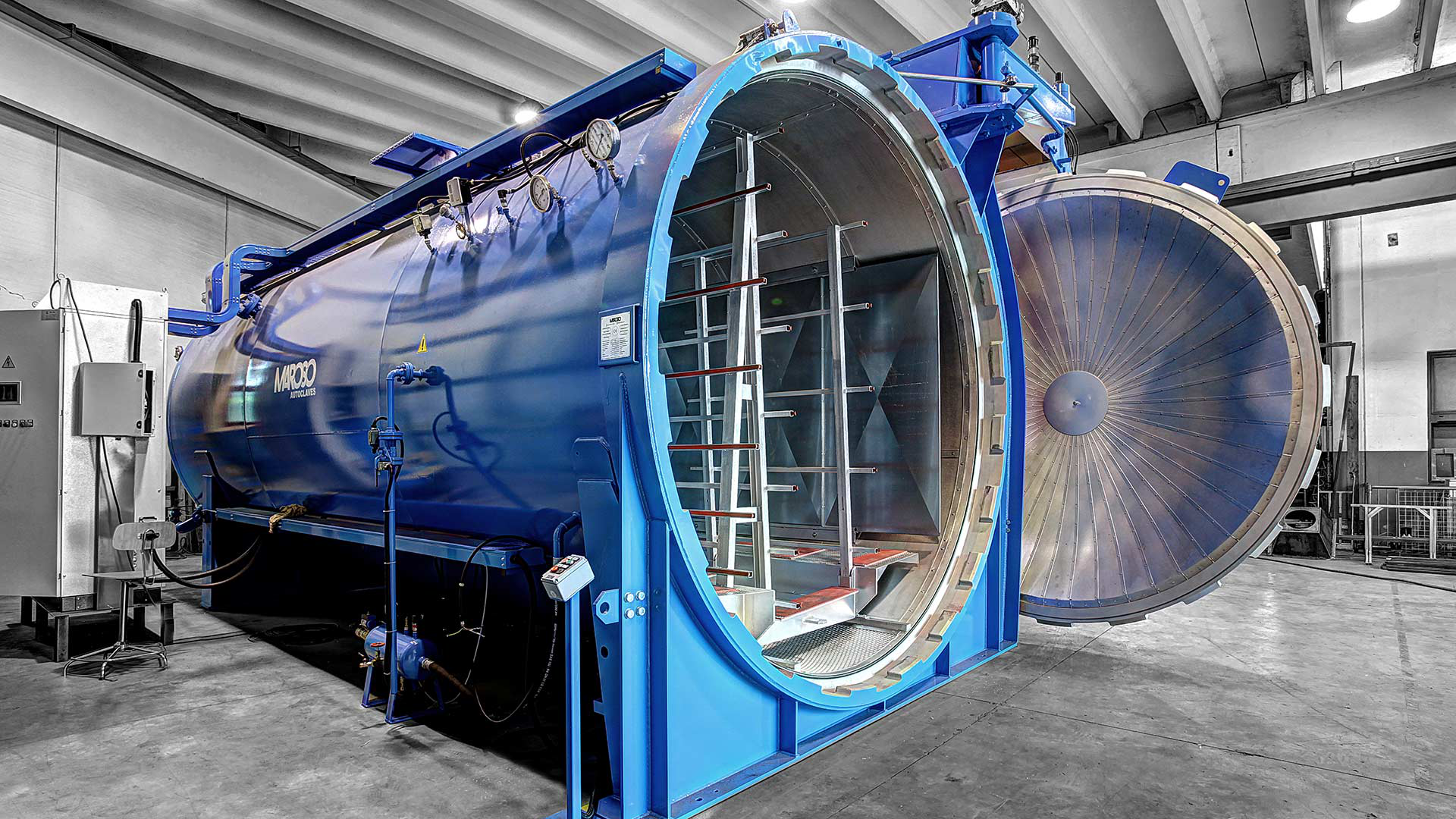
Vulcanization Autoclaves
Maroso autoclaves, through the vulcanization with direct steam or hot air recirculation, allows the rubber covering of: cylinders, industrial technical components, high pressure pipe for the Oil&Gas sector and the tires reconstruction. The standard production refers to the manufacturing processes for which is considered the injection of direct steam and/or mixes air/steam. When required, the material inside the autoclave can be subjected to cooling cycles.
These autoclaves are complete of loading and unloading system, or automated. The machines are designed in accordance to the customer’s requirements and to the productive processes of the different application fields. The autoclave is designed according to the customer’s requirements that, by a direct contact with our technicians, is followed from the design phase to the machine delivery. We use quality components and the most advanced technologies, guaranteeing the autoclave long life through time.
Autoclaves for Marble
Especially known by marble, ceramic conglomerate, porcelain stoneware, conglomerate compaction companies etc. Maroso autoclaves can be designed in various diameter sizes and length, foreseeing specific cycle loading quantities, guaranteeing the maximum efficiency and uniformity in the different process conditions. Maroso is able to design autoclaves complete of washing tank and rinsing nozzles, in line and with double door, in accordance to the customer’s requirements.
Autoclaves for Methacrylate Industry
Maroso designs autoclaves conceived for the methacrylate polymerization. The technological evolution of the sector, together with the experience acquired, allowed to successfully design and produce machines of different sizes and production capacities, process technologies and technical assistance. The handcrafts process takes into account the handcrafts characteristics, thicknesses and the different resins needed for the polymerization. It concerns complex technological aspects, for which Maroso produced machineries, demonstrating a high company professionality together with the achieved qualitative level.
Autoclaves for Food Industry
Maroso designs autoclaves conceived for food pasteurization and sterilization, allowing a better food conservation.
Through the pasteurization inside the autoclave at a temperature that goes from 60°C to 85°C for some minutes, we eliminate the organic liquids microflora, keeping both the physiochemical properties and the taste unchanged. This process, followed by a quick product cooling, aims to avoid that high temperatures excessively damage the product organoleptic and nutritional properties. Through the steam sterilization inside the autoclave we obtain an efficient microbicide action given by the heat at a predetermined temperature. The purpose is to correctly sterilize, preserve and guarantee the product health.
References
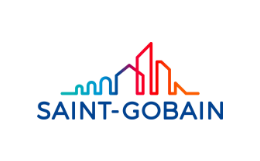
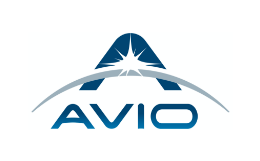
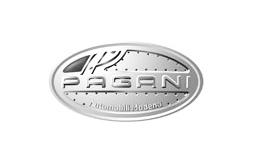
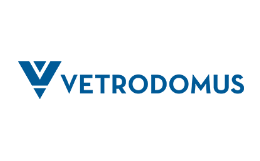
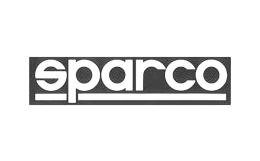
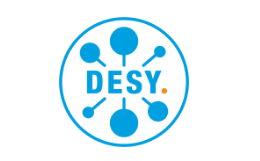
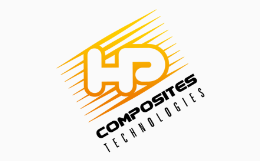
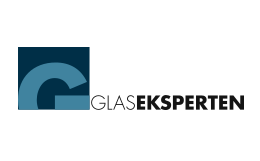
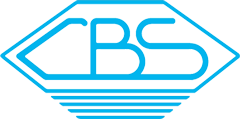
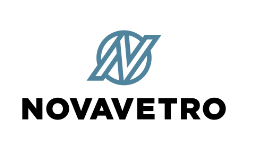
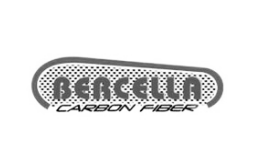
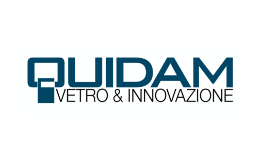